CANPACK Reports Full Year 2020 Results and Provides Q1 2021 Update
May 27, 2021
Krakow, Poland, May 27, 2021 — CANPACK (the “Company” or the “Group”), a global manufacturer of aluminum beverage cans and packaging solutions for the beverage and food industry, is pleased to announce, on a U.S. GAAP basis, with U.S. dollars (defined as “$”) as the reporting currency, its full year combined results for the year ended December 31, 2020 (“FY2020”) and its trading update for Q1 2021.
Full Year 2020 Highlights
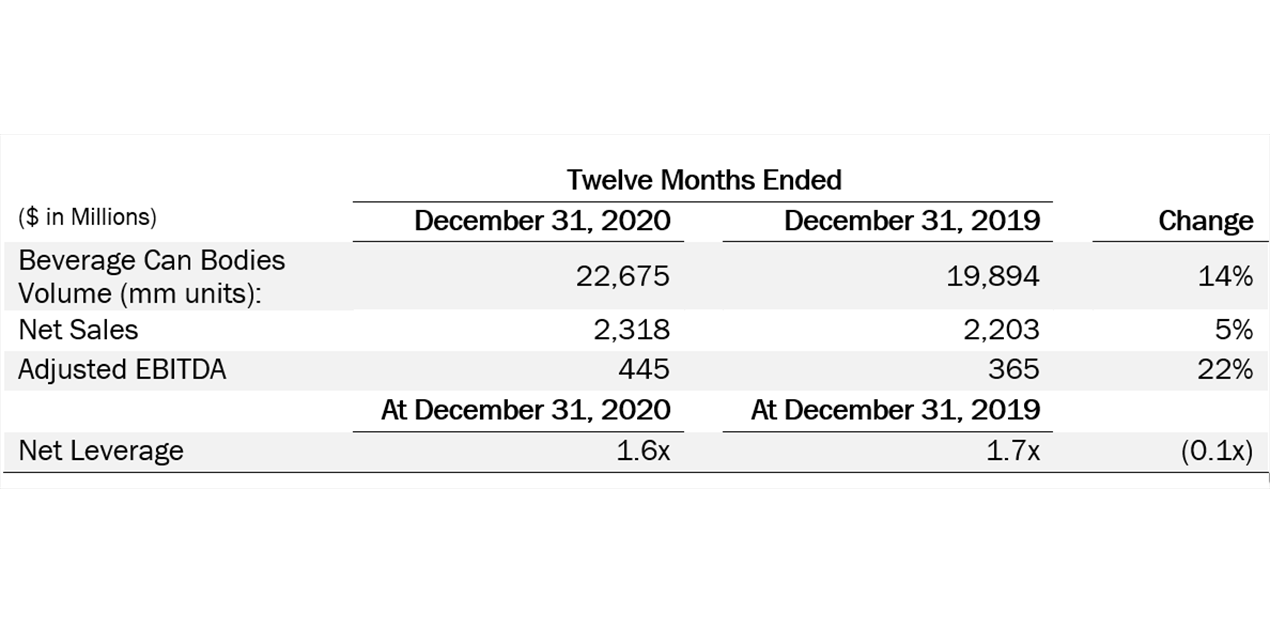
- During the twelve months ended December 31, 2020, beverage can bodies volumes grew 14% year-over-year, driven by significant growth in South America and Europe. During the year, consumers switched to beverage cans as the preferred option for at-home consumption. This was particularly true for beer, which saw increased sales in off-premise channels, such as grocery stores, supermarkets and discount stores, as at-home consumption increased. On-premise channels where beverage cans are less prevalent, such as bars, restaurants and pubs, realized weaker performance during 2020 given lockdown measures related to COVID-19 as compared to the twelve months ended December 31, 2019. In Q1, Q3 and Q4 2020, beverage can bodies volumes were significantly higher than corresponding periods in 2019 by more than 20%. This strong performance resulted from (i) increased production volumes from our new Czech Republic facility, which began production in June 2020, (ii) full year utilization of our Colombia facility, (iii) increased demand from the U.S. customer base, which was served by shipping cans from our facilities in South America, Asia and Europe and (iv) improved utilization of beverage can capacity at various CANPACK locations. In Q2 2020, beverage can bodies volumes declined by 7% year-over-year due to COVID-19 restrictions.
- Our first beverage can investment in the United States (in Olyphant, Pennsylvania) is on-track with the initial project schedule and is expected to stay within the approved budget. We anticipate beginning production as initially estimated in Q4 2021.
- Net sales increased 5% year-over-year, driven by higher beverage can volumes and a positive impact from currency exchange rate differences. However, net sales were partially offset mainly by lower year-over-year LME levels, local currency devaluation compared to USD in certain countries (mainly Brazil and Russia) and a change in product mix due to growth in smaller beverage cans, which have lower aluminum weight.
- Cost of sales increased 3% year-over-year, driven by higher beverage can volumes and currency exchange rate differences charged by suppliers. This was partially offset mainly by lower year-over-year LME levels, local currency devaluation compared to USD in certain countries (mainly Brazil and Russia) and a change in product mix due to growth in smaller beverage cans, which have lower aluminum weight.
- Adjusted EBITDA increased to $445 million in 2020 compared to $365 million in 2019 (+22%), mainly driven by higher volumes in beverage cans, improved productivity of our greenfield investments in Colombia, the Netherlands and the Czech Republic, tight cost controls, a net positive impact from currency exchange rate differences and a one-off gain in SG&A (see Note 23 of the 2020 U.S. GAAP combined financial statements for details).
- Capital expenditures increased to $371 million in 2020 compared to $190 million in 2019. This increase in capital expenditures was mainly driven by an initial investment in the U.S. beverage can facility in Olyphant, Pennsylvania (which is now nearing completion), the Czech Republic investment (which began production in June 2020) and the capacity expansion project in Colombia.
- Net cash provided by operating activities increased by $40 million to a net inflow of $320 million in 2020 compared to a net inflow of $280 million in 2019. This increase in cash provided by operating activities was primarily due to higher adjusted EBITDA, partially offset by the impact of higher working capital employed in the business as a result of increased sales.
- Free cash flow was positive, representing a cash inflow of $6 million in 2020 compared to a cash inflow of $146 million in 2019. In 2020, higher adjusted EBITDA relative to 2019 was more than offset by a $181 million increase in capital expenditures in 2020 relative to 2019.
Q1 2021 Highlights

- During the three months ended March 31, 2021, beverage can bodies volumes grew 21% year-over-year. Consumers have continued to switch to beverage cans as the preferred option for at-home consumption. This was particularly true for beer, which saw increased sales in off-premise channels, such as grocery stores, supermarkets and discount stores, as at-home consumption increased. On-premise channels where beverage cans are less prevalent, such as bars, restaurants and pubs, realized weaker performance during Q1 2021 given restrictions related to COVID-19 as compared to the three months ended March 31, 2020. CANPACK’s strong volume performance resulted from (i) increased production volumes from our new Czech Republic facility, which began production in June 2020, (ii) capacity expansion in Colombia, (iii) increased demand from the U.S. customer base, which was served by shipping cans from our facilities in Asia, South America and Europe and (iv) all capacities being sold out due to increased demand in Europe and South America.
- Net sales increased 21% year-over-year. This strong performance was driven by 21% growth in beverage can bodies volumes, 16% net sales growth in the Glass and Food and Industrial Packaging steel can businesses and higher LME levels in Q1 2021 compared to Q1 2020, partially offset mainly by a lower impact from the currency exchange rate differences during the three months ended March 31, 2021 compared to the corresponding period in 2020.
- Cost of sales increased 24% year-over-year due to increased beverage can volumes and a negative impact from aluminum price given higher LME levels during Q1 2021 compared to Q1 2020. This was partially offset mainly by a lower impact from the currency exchange rate differences charged by suppliers during the three months ended March 31, 2021 compared to the corresponding period in 2020.
- Adjusted EBITDA increased to $127 million in Q1 2021 compared to $113 million in Q1 2020 (+12%), driven by higher beverage can volumes. Results were partially offset mainly by the lower net impact from currency exchange rate differences and higher labor costs as a result of inflationary adjustments.
- Capital expenditures decreased to $44 million in Q1 2021 compared to $83 million in Q1 2020. This lower level of capital expenditures was mainly due to lower spend for our U.S. greenfield project in Olyphant, PA during the three months ended March 31, 2021 compared to capital expenditures spent during the three months ended March 31, 2020, which included our Czech Republic greenfield project.
- Net cash provided by operating activities increased by $48 million to a net inflow of $66 million in Q1 2021 from a net inflow of $18 million in Q1 2020. This increase in cash provided by operating activities was mainly due to higher adjusted EBITDA and lower working capital employed during the three months ended March 31, 2021 compared to the corresponding period in 2020.
- Free cash flow improved by $90 million year-over-year from a cash outflow of $54 million in Q1 2020 to a $36 million cash inflow in Q1 2021. This performance was due to higher adjusted EBITDA, lower working capital employed and lower capital expenditures during the three months ended March 31, 2021 compared to the corresponding period in 2020.
New Capacity Announcements
As demand for aluminum beverage can bodies and ends continues to outstrip supply across North America, we have decided to invest in a new 3-line beverage can bodies facility in Muncie, Indiana. This new facility is expected to be operational beginning in Q4 2022 and is currently backed by long-term contracts signed with multiple customers. During the last several months, we have increased our customer portfolio in the U.S. from three to eight. The total estimated investment for this facility is approximately $380 million. We will also invest an additional $10 million to expand ends production capacity at the Olyphant, PA facility in support of this new investment.
In addition to the above, due to increased demand for aluminum beverage can bodies and ends in the Northeastern U.S. region, we have decided to invest in a fourth line at our Olyphant facility. This incremental investment is estimated at $104 million and is expected to be finalized in Q4 2022.
Chief Executive Officer, Roberto Villaquirán, Commented:
“We are delighted to deliver a strong performance across our businesses. This was supported mainly by our continued market leading growth coupled by strict cost control and operational efficiency gains. With sustainability and innovation at the core of our strategy and differentiation, CANPACK is proud to be a leader in creating what we believe is the perfect platform and enabler for FMCG and brand owners to excel.”
About CANPACK
CANPACK Group, part of Giorgi Global Holdings, Inc, is a global manufacturer of aluminum beverage cans and packaging solutions for the food and beverage industries, as well as glass bottles and metal closures. Headquartered in Krakow (Poland), CANPACK employs nearly 8,000 people worldwide and has operations in 17 countries. For more information, visit www.canpack.com.
Conference Call Details
The Company will host a conference call at 14:00 BST / 15:00 CET / 09:00 EDT on Thursday May 27, 2021 to discuss its financial results with the investment community. Investors and analysts wishing to attend this event can request registration via email at IR@canpack.com or click on the following link.
More detailed financial information can be found on the Company’s IR website at the Financial Results and Bondholder Downloads section (click here to gain access).
Forward-Looking Statements Disclaimer
These forward-looking statements can be identified by the use of forward-looking terminology, including the terms “anticipate,” “assume,” “expect,” “suggests,” “plan,” “believe,” “intend,” “estimates,” “targets,” “projects,” “forecasts,” “should,” “could,” “would,” “may,” “will” and other similar expressions or, in each case, their negative or other variations or comparable terminology.
All statements other than statements of historical facts included in this document, including, without limitation, statements regarding our future financial position, risks and uncertainties related to our business, strategy, capital expenditures, projected costs and our plans and objectives for future operations, may be deemed to be forward-looking statements. These forward-looking statements are subject to a number of risks and uncertainties.
We caution you that forward-looking statements are not guarantees of future performance and that our actual results of operations, financial condition and liquidity, and the development of the industry in which we operate, may differ materially from those made in or suggested by the forward-looking statements contained in this document. In addition, even if our results of operations, financial condition and liquidity, and the development of the industry in which we operate are consistent with the forward-looking statements contained in this document, those results or developments may not be indicative of results or developments in subsequent periods.
Any forward-looking statement that we make in this document speaks only as of the date on which it is made, and we do not intend to update such statements. Comparisons of results for current and any prior periods are not intended to express any future trends or indications of future performance, unless expressed as such, and should only be viewed as historical data. By their nature, forward-looking statements involve risks and uncertainties because they relate to events and depend on circumstances that may or may not occur in the future and may not be within our control.
Moreover, the Company operates in a very competitive and rapidly changing environment. New risk factors emerge from time to time, and it is not possible for us to predict all such risk factors, nor can we assess the impact of all such risk factors on our business or the extent to which any factor, or combination of factors, may cause actual results to differ materially from those contained in any forward-looking statements. Given these risks and uncertainties, you should not place undue reliance on forward-looking statements as a prediction of actual results.
Non-GAAP Measures
The above press release contains certain financial measures and ratios, including adjusted EBITDA, free cash flow, net leverage, changes in working capital, beverage can bodies volume and capital expenditures, that are not required by, or presented in accordance with, U.S. GAAP (the “Non-GAAP Measures”).
We present these Non-GAAP Measures because they are measures that our management uses to assess operating performance and liquidity, and we believe that they and similar measures are widely used in our industry as supplemental measures of performance and liquidity. These measures may not be comparable to other similarly titled measures of other companies and are not measurements under U.S. GAAP or other generally accepted accounting principles.
Non-GAAP Measures and ratios are not measurements of our performance or liquidity under U.S. GAAP and should not be considered as alternatives to net income or any other performance measures derived in accordance with U.S. GAAP or as alternatives to cash flow from operating, investing or financing activities.
Contacts:
CANPACK IR team
Lorenzo Ruffatti
Group Investor Relations Manager
Marta Kopcik
Group Communications Manager
Email: IR@canpack.com
CANPACK IR Advisor
Li Zhao – Maitland/AMO
Phone: +44 (0) 207 379 5151
Email: canpack@maitland.co.uk